The transition to renewable energy is more than a trend; it’s a necessity. Among the various renewable energy sources, biogas holds a unique position. Derived from organic waste, biogas can be upgraded to Renewable Natural Gas (RNG), a cleaner and more efficient fuel. However, the journey from raw biogas to RNG is fraught with challenges, primarily because biogas is not a one-size-fits-all commodity. In this comprehensive guide, we’ll delve into the critical factors that influence the choice of a biogas conditioning system, including feedstock type, scale, and end-use application.
Understanding the Basics of Biogas Conditioning
Biogas conditioning is the process of treating and purifying raw biogas to remove various impurities such as hydrogen sulfide (H2S), carbon dioxide (CO2), water vapor, and sometimes ammonia (NH3). The ultimate goal is to produce a cleaner, more efficient fuel that can be used in a variety of applications, from electricity generation to RNG injection into the gas grid.
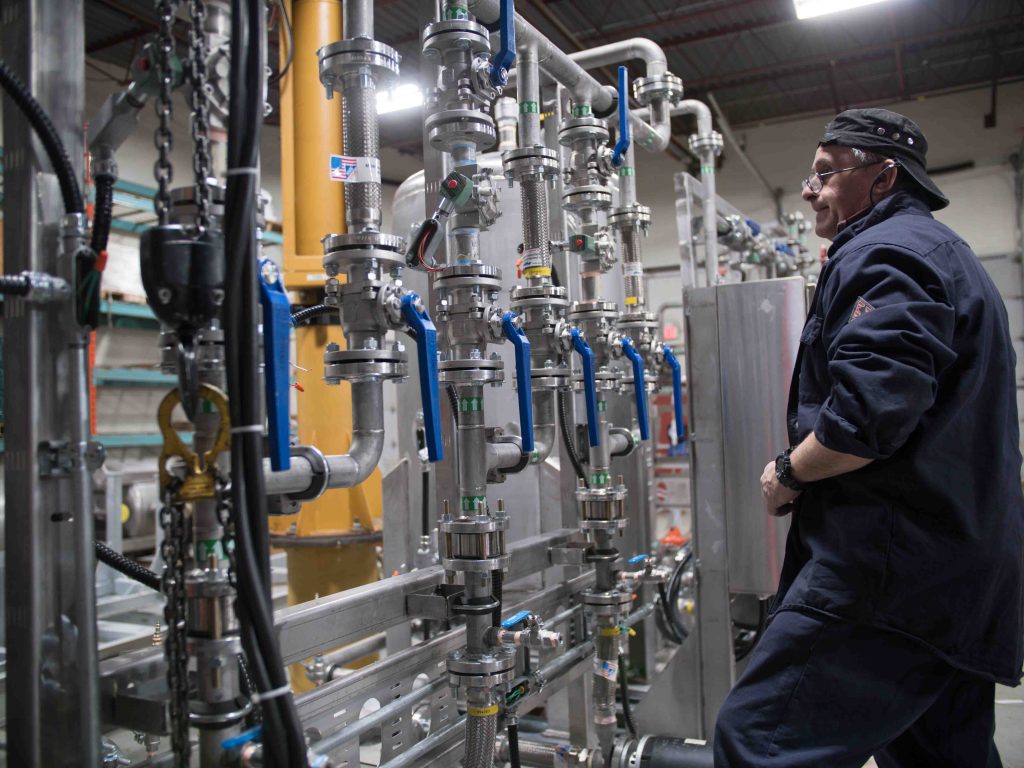
Feedstock Types and Their Implications
The type of organic matter used to produce biogas significantly impacts the composition of the gas. Here’s a closer look at some common feedstock types:
Agricultural Digester Biogas
Derived from animal manure and agricultural waste, this type of biogas often contains higher levels of ammonia. Specialized NH3 removal systems may be necessary to treat this gas effectively.
Source-Separated Organic (SSO) Waste
Biogas from SSO waste can vary widely in composition, depending on the types of organic waste included. It may require a more flexible conditioning system capable of handling a range of impurities.
Wastewater Treatment Plant (WWTP) Biogas
Produced from sewage sludge, this biogas often contains higher levels of hydrogen sulfide. Advanced H2S removal systems are usually required to treat this type of gas.
Landfill Gas
Landfill gas can contain a variety of impurities, including volatile organic compounds (VOCs). Specialized activated carbon polishing units may be necessary for this type of feedstock.
Scale of Operation: One Size Doesn’t Fit All
The scale of your biogas production will influence the type of conditioning system you need. Smaller operations may require compact, modular systems, while larger facilities might benefit from more extensive, integrated solutions. GraniteFuel’s biogas compression and blower systems are designed to meet the needs of operations of all sizes, ensuring efficient and reliable performance.

End-Use Application: Purity Requirements and Challenges
The intended use for the conditioned biogas will significantly influence your choice of a conditioning system. Different applications have different purity requirements:
RNG for Pipeline Injection
Injecting RNG into the gas grid requires the highest purity levels. The gas must meet stringent specifications, often requiring additional treatment steps like activated carbon polishing. GraniteFuel’s advanced polishing units are designed to remove any remaining trace impurities, ensuring the RNG meets the highest quality standards.
Onsite Electricity Generation
When biogas is used for onsite electricity generation, the purity requirements may be less stringent. However, impurities like H2S can corrode engine parts, leading to increased maintenance costs. Therefore, effective H2S removal systems are crucial even for this application.
Unique Technologies: Regenerative Temperature Swing Adsorption
GraniteFuel Engineering specializes in Regenerative Temperature Swing Adsorption, a unique technology that offers higher efficiency and lower operational costs compared to traditional methods. This advanced method sets new standards for efficiency and reliability in biogas upgrading.
Making an Informed Decision
Choosing the right biogas conditioning system is a complex but crucial task. It requires a deep understanding of various factors, from the type of feedstock and scale of operation to the intended end-use application. By considering these elements and consulting with experts in the field, you can make an informed decision that meets your specific needs.
GraniteFuel Engineering offers a range of advanced biogas conditioning systems and technologies, designed to meet the unique challenges of different feedstocks, scales, and applications. With our expertise and cutting-edge solutions, you can be confident in your choice of a biogas conditioning system that will deliver reliable, high-quality results.