In the realm of renewable energy, biogas stands out as a promising and sustainable energy source. Derived from organic materials, biogas can be transformed into a high-quality fuel suitable for various applications. However, this transformation requires a series of intricate processes, each with its unique purpose and methodology. In this article, we delve into the differences between biogas pretreatment, conditioning, and upgrading, and spotlight GraniteFuel Engineering’s specialized approach to each.
Biogas Pretreatment: The Initial Refinement
What is Biogas Pretreatment? Biogas pretreatment is the first step in refining raw biogas produced from anaerobic digestion. It involves the removal of initial impurities and contaminants that might be present.
Common pretreatment processes include:
- Moisture Removal (Dehydration): Extracting water content to prevent downstream equipment corrosion and improve combustion efficiency.
- Particulate Removal (Filtration): Filtering out solid particles that could damage or clog equipment.
- Hydrogen Sulfide (H2S) Removal: Using chemical or biological methods to eliminate H2S, a corrosive and toxic gas.
GraniteFuel’s Approach to Biogas Pretreatment: GraniteFuel Engineering employs state-of-the-art technologies to ensure efficient and thorough pretreatment. Their systems are designed to handle varying biogas compositions, ensuring optimal removal of impurities and setting the stage for subsequent processes.
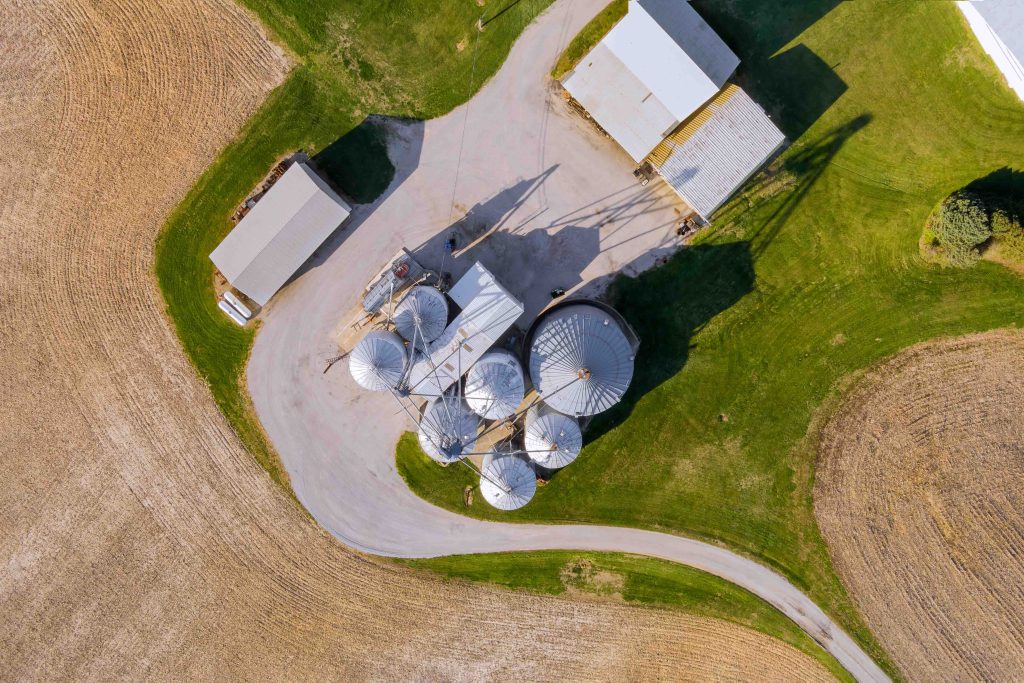
Biogas Conditioning: Tailoring for Specific Applications
What is Biogas Conditioning? Biogas conditioning encompasses a range of processes to treat and refine biogas to meet specific quality or application standards.
Conditioning can involve:
- Temperature Control: Adjusting the biogas temperature to optimize subsequent processes.
- Pressure Control: Modifying the biogas pressure for specific applications or equipment.
- Contaminant Removal: Extracting impurities like VOCs, siloxanes, and additional H2S or CO2, depending on the biogas’s intended use.
GraniteFuel Biogas Conditioning Expertise: With a deep understanding of the intricacies of biogas, GraniteFuel Engineering designs systems that prioritize both the lowest possible operating costs and system reliability. Their conditioning solutions tailor biogas perfectly for its intended application, whether for direct combustion, gas engines, or further upgrading.
Biogas Upgrading: Elevating to Renewable Natural Gas
What is Biogas Upgrading? Biogas upgrading is the enhancement of biogas’s methane content by removing CO2 and other impurities, producing renewable natural gas (RNG) of comparable quality to natural gas.
Common upgrading techniques include:
- Water Scrubbing: Using water to absorb CO2
- Membrane Separation: Utilizing selective permeability to separate methane from CO2
- Chemical Absorption: Using chemicals to selectively absorb CO2
GraniteFuel’s Specialization: GraniteFuel Engineering stands out in the biogas upgrading sector with its unique approach. Instead of the commonly used pressure swing adsorption (PSA), GraniteFuel employs temperature swing adsorption (TSA). TSA involves regenerating the adsorbent material by changing the temperature, making it a more energy-efficient and effective method for biogas upgrading. This innovative approach ensures higher methane recovery rates and superior RNG quality.
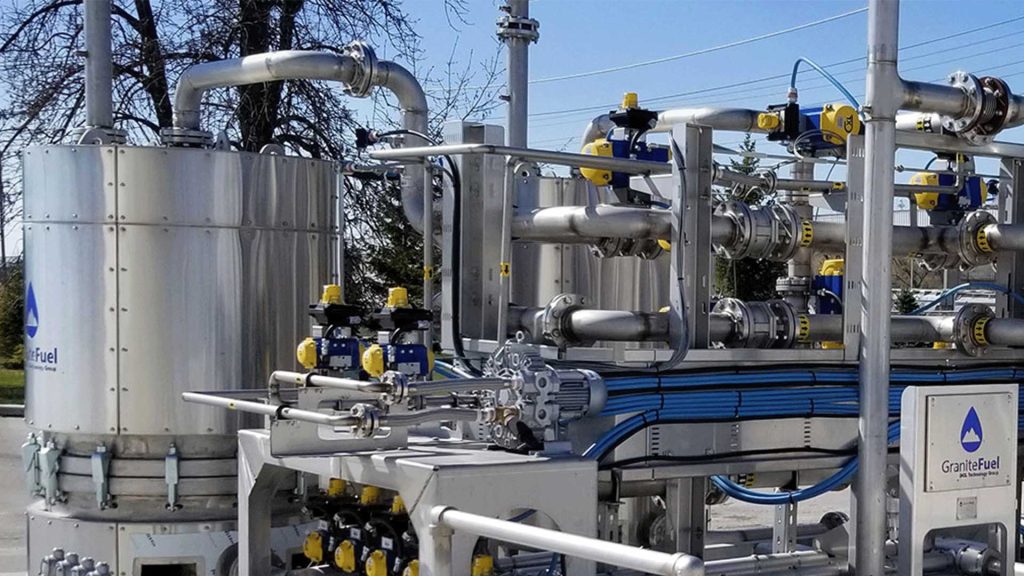
Temperature Swing Adsorption (TSA) vs. Pressure Swing Adsorption (PSA)
While PSA is a widely recognized method for gas separation, TSA offers distinct advantages, especially in the context of biogas upgrading. In PSA, the regeneration of the adsorbent material is achieved by reducing the pressure. In contrast, TSA regenerates the adsorbent by changing the temperature.
GraniteFuel’s TSA Advantage: GraniteFuel’s adoption of TSA technology underscores their commitment to innovation and efficiency. TSA allows for:
- Higher Methane Recovery: By optimizing the adsorption and desorption cycles, TSA can achieve higher methane recovery rates.
- Energy Efficiency: TSA systems can be designed to utilize waste heat from other processes, making them more energy-efficient.
- Operational Flexibility: TSA provides more flexibility in terms of operating conditions, allowing for better adaptation to varying biogas compositions.
Membrane Separation: GraniteFuel’s Choice for Biogas Upgrading
Membrane separation is a process that uses semi-permeable membranes to separate and concentrate specific components from a mixture. In the context of biogas upgrading, it’s employed to enhance the methane content by separating it from carbon dioxide (CO2) and other impurities.
How It Works: The principle behind membrane separation is selective permeability. The membranes used in biogas upgrading are designed to allow certain gases (like methane) to pass through more readily than others (like CO2). When biogas is passed through these membranes, methane is concentrated on one side, while CO2 and other impurities are reduced on the other.
Advantages:
- Efficiency: Membrane systems can achieve high methane purities and recoveries, making them suitable for producing high-quality RNG.
- Modularity: Membrane systems are modular, allowing for easy scalability. As biogas production increases, additional membrane modules can be added to handle the increased volume.
- Low Maintenance: With fewer moving parts and no chemicals involved, membrane systems typically require less maintenance and have longer operational lifespans compared to other upgrading methods.
- Environmental Friendliness: Membrane separation doesn’t rely on chemicals or generate waste streams, making it an environmentally friendly option.
GraniteFuel Engineering has recognized the potential of membrane separation and has integrated it into their biogas upgrading solutions. Their systems maximize methane recovery while ensuring the highest RNG quality. By leveraging advanced membrane technologies, GraniteFuel offers a solution that is both efficient and sustainable, aligning with their commitment to innovation and environmental responsibility.
Biogas Pretreatment to Upgrading
Biogas holds immense potential as a renewable energy source. However, unlocking this potential requires expertise, innovation, and a deep understanding of the processes involved. GraniteFuel Engineering, with its specialized approach to biogas pretreatment, conditioning, and upgrading, is at the forefront of this industry. By prioritizing efficiency, reliability, and innovation, GraniteFuel ensures that producers of biogas and RNG operators achieve the highest return on their RNG investments.